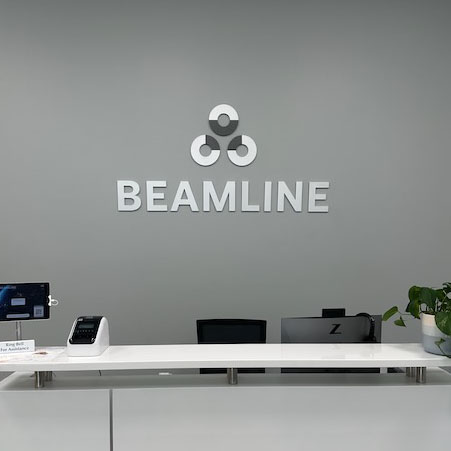
Achieving ITAR compliance isn't just a bureaucratic checkbox for a semiconductor testing lab like Beamline's – it's a commitment to national security and customer trust. Our work to become ITAR-registered touched every aspect of our operations. From controlling who enters our lab to how we store customer materials, we had to rethink procedures and reinforce our culture of compliance. In this article, we share our experience navigating the International Traffic in Arms Regulations (ITAR) maze – why it matters, the challenges we faced, and what it really takes for a lab to be effective in ITAR compliance.
In the world of semiconductors, sensitive technology often straddles commercial and defense uses. ITAR is the U.S. regulation that safeguards defense-related technology from falling into unauthorized hands. For a semiconductor analysis lab, this means any data or sample tied to a defense program must be handled with extreme care – only U.S. Persons (U.S. citizens or permanent residents, with few other exceptions) can access it, and it mustn't be exported or even shown to a foreign national without government approval.
The stakes are high: violations can incur fines up to $1 million per incident and even 10 years in prison. In one recent case, Boeing faced a $51 million penalty for ITAR violations, and another major contractor was fined $200 million. Clearly, ITAR compliance is not optional if you deal with controlled tech – it's legally mandatory and crucial to avoiding business-crippling penalties.
Key Takeaways
The recent CHIPS Act incentives in the U.S. are creating both opportunities and challenges for ITAR compliance:
The CHIPS Act is spurring new domestic chip factories and aiming to reduce reliance on overseas suppliers. This is great news for American labs, since more U.S.-made chips mean fewer jurisdictional hurdles.
After the last U.S. semiconductor boom decades ago, and the gradual offshoring that happened for the decades after, many experienced engineers retired or left the industry. Projections show the industry will need over 1 million additional skilled workers by 2030.
For Beamline, this environment creates a dual challenge: implementing rigorous ITAR controls while also addressing the talent shortage. We need to hire and train with intention, balancing the requirement for U.S. persons with anti-discrimination requirements, all in a market where semiconductor (and especially SIMS) talent is both limited and in high demand.
Like major semiconductor manufacturers, we've established workforce-development partnerships with universities including Arizona State University and Northern Arizona University to help build the secure talent pipeline the industry desperately needs.
Semiconductor testing labs, and SIMS labs specifically, are a critical and often overlooked link in the supply chain for defense electronics. Beamline's ITAR program represents our commitment to the resilience of the U.S. semiconductor industry.
The CHIPS Act is driving renewed investment in domestic semiconductor manufacturing
While the paperwork itself is not complicated, getting officially "ITAR registered" through the State Department's Directorate of Defense Trade Controls (DDTC) was a significant project that required changes at every level of our lab's operations. That acknowledgement required we attest to many aspects about the business, from ownership to operational processes, and invites scrutiny from agencies that might not otherwise know Beamline exists. Here's how we implemented a comprehensive ITAR program:
As part of registering Beamline with the DDTC as an entity handling defense-related materials and technical data, we appointed an Empowered Official – an internal champion with authority and responsibility to oversee export control compliance and sign off on licenses. This gave us a formal structure for accountability.
While we already take sample handling and archiving very seriously, and have established procedures as part of our ISO/IEC 17025 accreditation, we established additional strict procedures for any ITAR-tagged samples entering our lab:
We upgraded our visitor management system to screen everyone who comes through the door:
Our lab already had good security posture, including badge-controlled access to all laboratory entrances and to rooms housing ITAR-sensitive equipment, plus alarms and cameras to monitor any attempt at unauthorized entry. But we reevaluated our physical security measures as part of our ITAR risk assessment and made targeted improvements where needed.
ITAR vs. EAR: What's the Difference?
Administered by the State Department, ITAR specifically covers defense articles and services listed on the U.S. Munitions List. It requires access be limited to U.S. Persons and imposes stricter penalties than the more general Export Administration Regulations (EAR).
These more general regulations cover a broader range of commercial items that have potential military applications, with somewhat less restrictive controls than ITAR.
Physical security is a key component of ITAR compliance
Perhaps the biggest challenge was ensuring our IT systems protect controlled technical data. ITAR requires all controlled data to stay on U.S. soil. We implemented a comprehensive approach:
By leaning into modern technologies, we are thinking not only about our compliance but also the compliance of our customers during the data delivery process.
Beamline's policy is to hire the best talent, and we're proud of our diverse team. But under ITAR, only U.S. Persons can work directly with ITAR-controlled projects. We revamped our hiring process to ensure compliance with this requirement while clearly separating our export control compliance and work authorization screening processes to ensure we do not discriminate against any potential employee.
We developed specialized ITAR training for every team member – from scientists to janitorial staff – so everyone understands:
This training is now part of onboarding and is refreshed annually.
Throughout our journey, we learned that ITAR compliance and registration presents significant operational burdens and challenges, for both small and large labs:
For small labs, having significant processes and actually following them often is difficult because of the technical and people infrastructure required. There is a tendency with these sorts of policies and procedures in the fragmented testing lab industry to adopt minimum policies required to say "compliant" without actually having the resources to follow them day-to-day.
On the other end of the spectrum, it's entirely possible to have a large lab vendor claim to be ITAR-compliant, but find out that may apply only to specific locations or services. Why the fine print? One reason is the people factor. Many big labs rely on a global talent pool to staff many niche techniques, including highly skilled scientists on H-1B visas or other work permits.
These employees – while experts in semiconductors – are legally considered foreign persons under ITAR and therefore cannot access ITAR-controlled projects without an export license. As a result, a large lab might say "ITAR work accepted here," but behind the scenes they have to ensure only certain U.S. employees handle it (perhaps shuffling projects to a particular office or team). Even if they can support the work, this can introduce delays, or worse, mistakes if the segregation isn't ironclad.
Verifying ITAR compliance requires thorough due diligence
Beamline's size and focus put it in a unique position. We are a reasonably sized lab compared to many in terms of headcount, which gives us resources to implement processes and track compliance. We also have the benefit of laser focus on advanced metrology (SIMS specifically) for the semiconductor industry, which allows our processes and procedures to be well thought out and reduces the amount of staff required to ensure smooth implementation. All of our staff are focused on this type of testing, which enables them to master the compliance processes and procedures.
To verify true compliance versus simply taking a lab's word for it, we recommend customers:
As part of Beamline's commitment, we invite our customers to visit/audit our lab and see for themselves, and we are happy to be transparent and share our policies and procedures for them to inspect.
Achieving ITAR compliance was a transformative journey for Beamline. It forced us to scrutinize and strengthen nearly every lab process, from the front door to the data server. The fragmented semiconductor supply chain and resurgence of U.S. chip manufacturing mean that this level of compliance is more important than ever – and also more challenging, given global partnerships and talent shortages.
We're proud to have built an environment where customers can trust that their sensitive projects will stay secure. What makes Beamline truly unique in the semiconductor testing space is our rare combination of deep technical expertise in SIMS analysis and rigorous ITAR compliance – ensuring customers get both superior analytical results and peace of mind regarding security.
For any organization wondering if the effort is worth it, we can say this: the confidence of being truly ITAR-compliant opens doors to projects and partnerships that simply wouldn't be possible otherwise. It's enabled Beamline to support cutting-edge semiconductor programs tied to national defense and to do so without hesitation or legal risk.
If you're working on advanced semiconductors and need a testing partner who "gets it" when it comes to export controls, Beamline is ready to help.
Note: Materials and data can be shared with foreign nationals or removed to foreign countries with an export license. Beamline's goal was to remove the need for export licenses, as they cause additional burden for both Beamline and our customers.